光伏组件制造中的相关技术问题
本文摘要:作者:天津力神电池股份有限公司 副总工程师/光伏事业部技术总监 于振瑞 在光伏产业链中,组件是直接面向终端客户的产品;而组件制造中...
2、原材料的选择与匹配
封装材料的选配对于最终的产品的技术性能与可靠性影响很大。电池片是最重要的原材料,电池片生产商除了测试电流、电压、功率等参数外,一般不全面控制Rs、Rsh、反向漏电流Irev等参数,即使有所控制标准也比较宽松。而这几个参数对于组件的可靠性、kWh/kW等具有直接的影响。另一方面,电池片的分选均是在STC条件下进行的,而大部分电池片在STC条件下分档后,在弱光下其电流和功率的一致性并不能很好地保持,这就造成了一个组件在实际野外运行时其中的电池片性能一致性不好,发电量较低和失效风险增加。
为了降低成本,"段栅"结构电池片正得到推广。研究表明,段栅结构可以缓解焊带/电池片焊接带来的应力,增加组件的可靠性。初步的数值估算也表明,电池片主栅线分段焊接不会带来封装损失的明显增大。然而,电池片正面段栅需要考虑温度循环条件下栅线的断裂或从Si片上脱层的可能性。这需要焊接工艺的改进才能完全避免这种潜在的失效隐患。
对于密封材料,目前广泛使用的EVA具有很高的可靠性和较低的成本,然而由于其中含有紫外稳定成分造成其短波光通过率较低。目前已经由EVA的替换材料能够克服这一缺点-有机硅胶(Silicone)、PVB、TPU等。这些材料一般具有极好的紫外透过率和密封效果,但其成本需要大幅度降低才能真正替代EVA。另一发展方向是对EVA进行改良,在EVA中加入某种光转换成份,把入射的紫外光下转换为可见光。为了实现这一目标,高效稳定的光转换剂以及如何把转换剂均匀地分散在EVA中是需要解决的关键问题。目前有很多研究机构正在开发光转换剂。
在表面镀减反膜的低铁钢化玻璃正在被越来越广泛地接受,然而,镀层的机械及化学稳定性需要进一步的确认;镀层表面的清洁问题也是需要解决的问题。普通的减反膜技术与纳米技术结合也许会产生一种新的技术-多功能减反转光膜。在半导体行业,硅基纳米材料具有很强的光学下转换特性,即可以把200-400nm的紫外光转换为600-900nm的可见光。减反膜本身也是硅基氧化物,二者结合在一起,理论上讲是完全可能的,关键是解决技术相容性的问题。
此外,一些新的封装部件如微型逆变器,DC/DC控制器等正在被一些厂家试用。这些部件赋予组件产品一些的新的功能,可以使组件输出交流电或稳定的直流电压,最大化地满足了客户的需求。然而要想大范围应用还需要大幅度地降低成本才有可能。
3、工艺的改善
降低封装损失是组件制造中一直追求的目标。封装损失的降低依赖于焊接工艺的优化、EVA胶联度的优化等。由于EVA的折射率是其胶联度的函数,合适的EVA胶联度有助于增加光的透过率。关于电池片与焊带之间的焊接长度,有两种不同的看法:一种认为应该严格控制虚焊,使得主栅线的焊接长度足够大;另一种观点认为,主栅线上采取"点焊"(即每隔一定间距焊接一段)方式不会造成明显的封装损失,并且对于缓解硅片的应力有利,可以增加组件的可靠性。据统计,在各类失效中,由于焊接和化学腐蚀造成的失效占80%以上的比例,因此这两道工序的控制对于组件可靠性也至关重要。优化焊接温度、焊接长度、EVA胶联度等是工艺改善的重要内容。
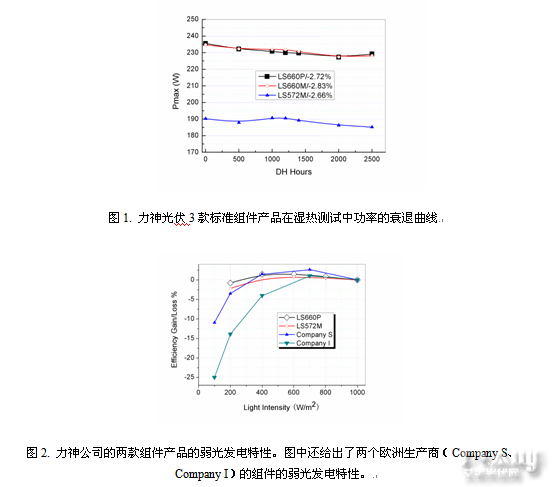
总之,先进的组件封装技术应该能保证稳定地生产出高质量组件产品。我们的实践表明,从组件制造的全过程(设计、原材料选配、工艺技术)细化并严格控制相关的技术指标,组件产品的性能得到稳定的大幅提高。图1、图2分别给出了我们的组件产品在湿热测试与弱光测试中的实际测量值。组件产品经过DH2500小时后其功率衰退小于2.83%,200W/m2弱光下的组件转换效率η'与STC下的组件转换效率η相比其损耗值

小于3%。另外在61kWh室外累计光照后LID衰退小于1.2%(单晶)和0.8%(多晶)。